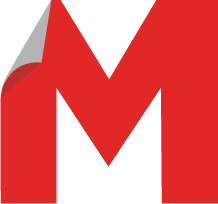
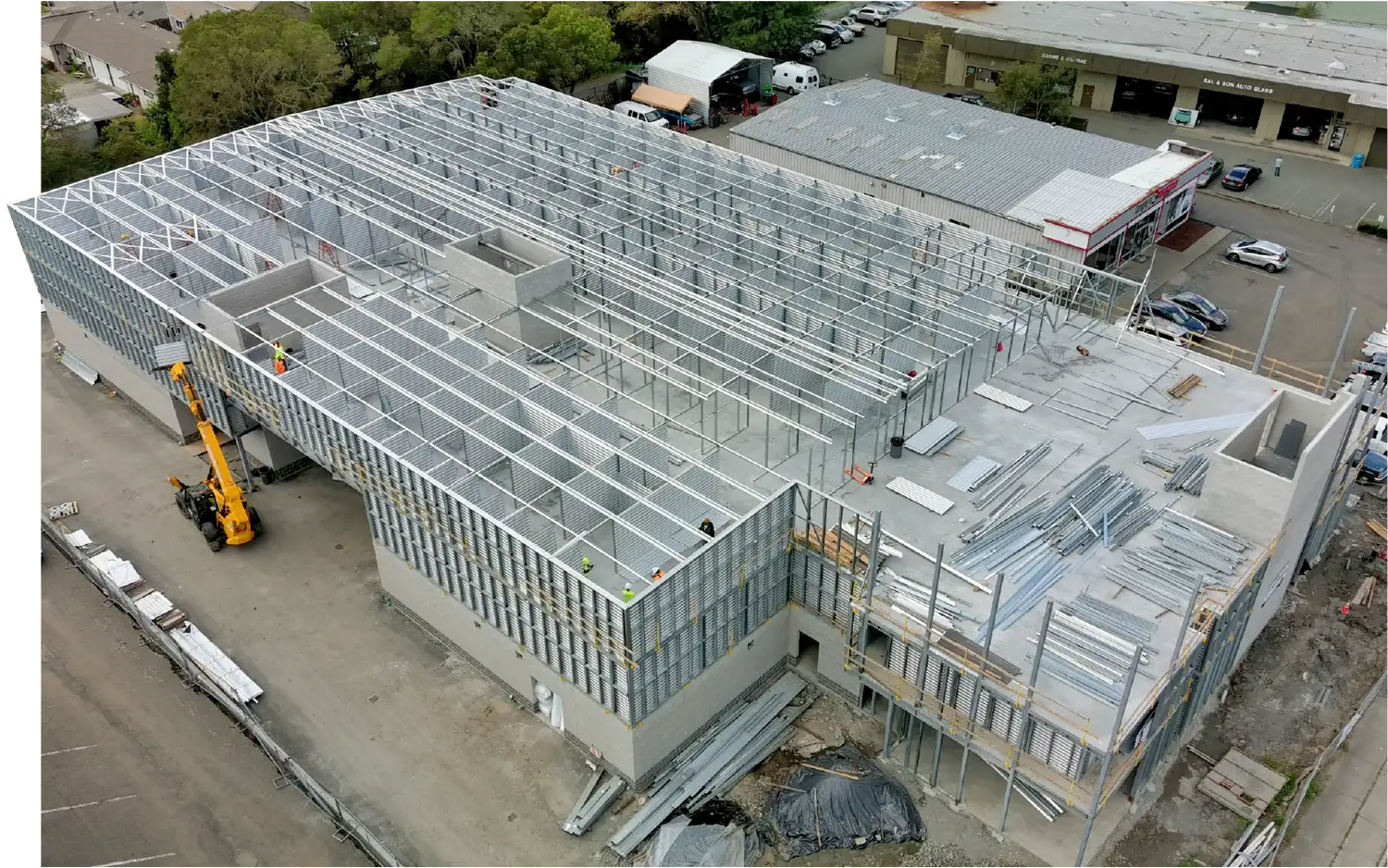
hen venturing into the construction of a multilevel self-storage facility, several designs and structural systems come into play, each with its own set of advantages and complexities. Let’s explore some of these systems and uncover their significance in today’s modern era.
Now, about lateral resistance: It’s especially important in areas prone to earthquakes, like the West Coast. Depending on factors like the number of stories, soil conditions, and exposure, extra measures may be needed. The U-panel sheathing can sometimes provide enough lateral resistance, but in cases where more is needed, flat-sheet steel or additional structural elements like masonry shear walls or steel brace frames may be added. However, designers usually avoid the flat-sheet approach due to issues with fastener spacing and aesthetics. These additional elements can affect things like corridor layout, door placement, and even future flexibility if unit sizes need to change.
Other lateral resistance strategies include masonry shear walls or engineered structural steel (“red iron”) brace frames. It’s worth mentioning that masonry shear walls and shafts have fire-resistant properties, which can be beneficial for meeting building codes. However, incorporating these elements can complicate construction timelines due to additional subcontractor coordination and fabrication processes. We advocate for early coordination with the structural design consultant when using brace frames or full-height masonry shear walls to vet out impacts to building design and unit layout. It should be noted that these types of lateral resistance elements can have an adverse impact on future flexibility if an operator were to want to reconfigure unit sizes in response to market conditions.
While the light gauge bearing wall system offers simplicity and efficiency, it’s essential to consider factors like lateral resistance and construction sequencing when planning multilevel storage facilities.
Post and beam systems offer a different approach compared to the light gauge bearing wall system, providing increased flexibility for future layout changes in storage units. Unlike the continuous bearing walls of the light gauge system, post and beam setups allow for more adaptable configurations. During construction, this setup also facilitates easier removal of snow, water, and debris until the perimeter walls and interior corridors are established.
An emerging variant of the post and beam system is the Alpha Framing system (see the photos for examples). This system employs factory-assembled, built-up light gauge columns arranged on a 10-foot grid to support concrete-filled steel beams. These beams, in turn, uphold concrete slab on composite metal deck floors, akin to traditional light gauge bearing wall designs. The Alpha Framing system marries the efficiency of light gauge framing with the flexibility and openness of post and beam layouts, bypassing the need for extensive structural steel components and associated fabrication processes.

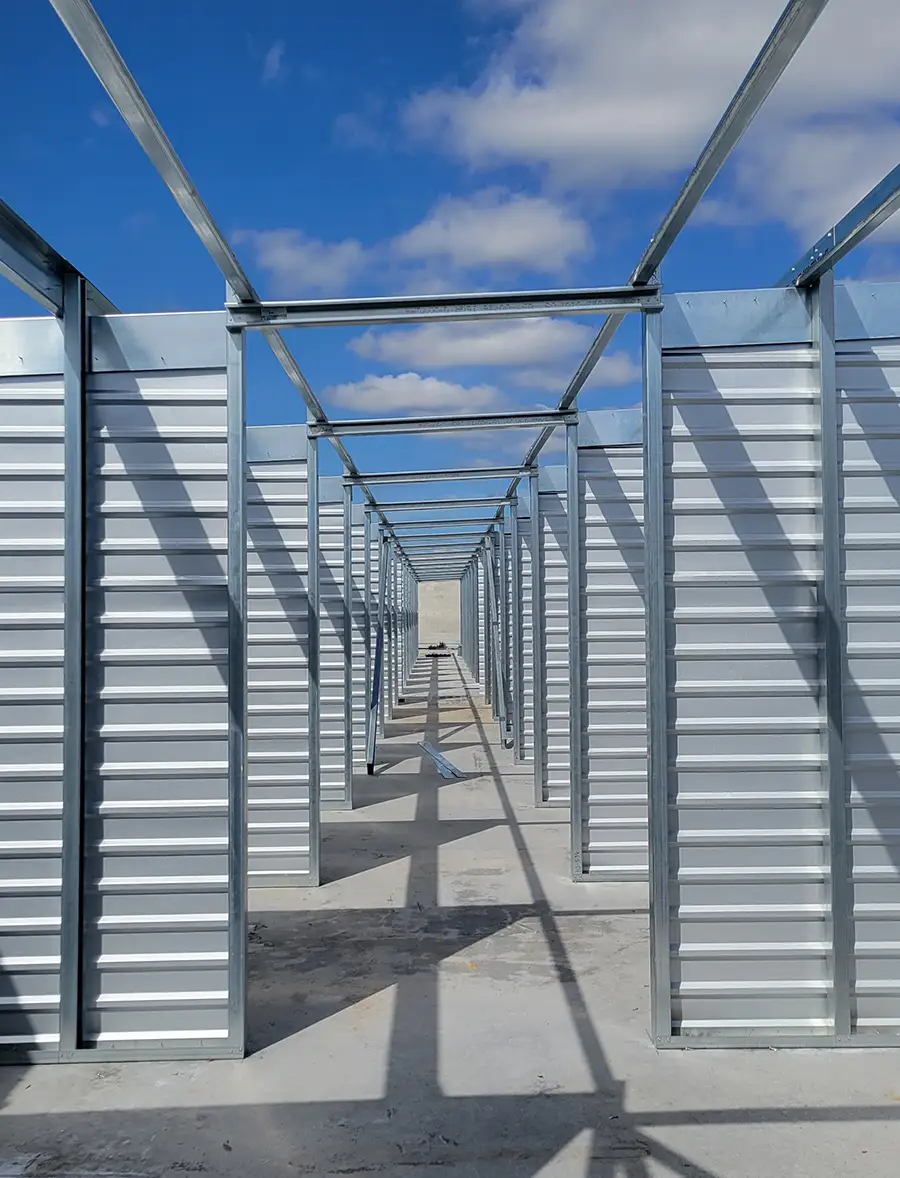
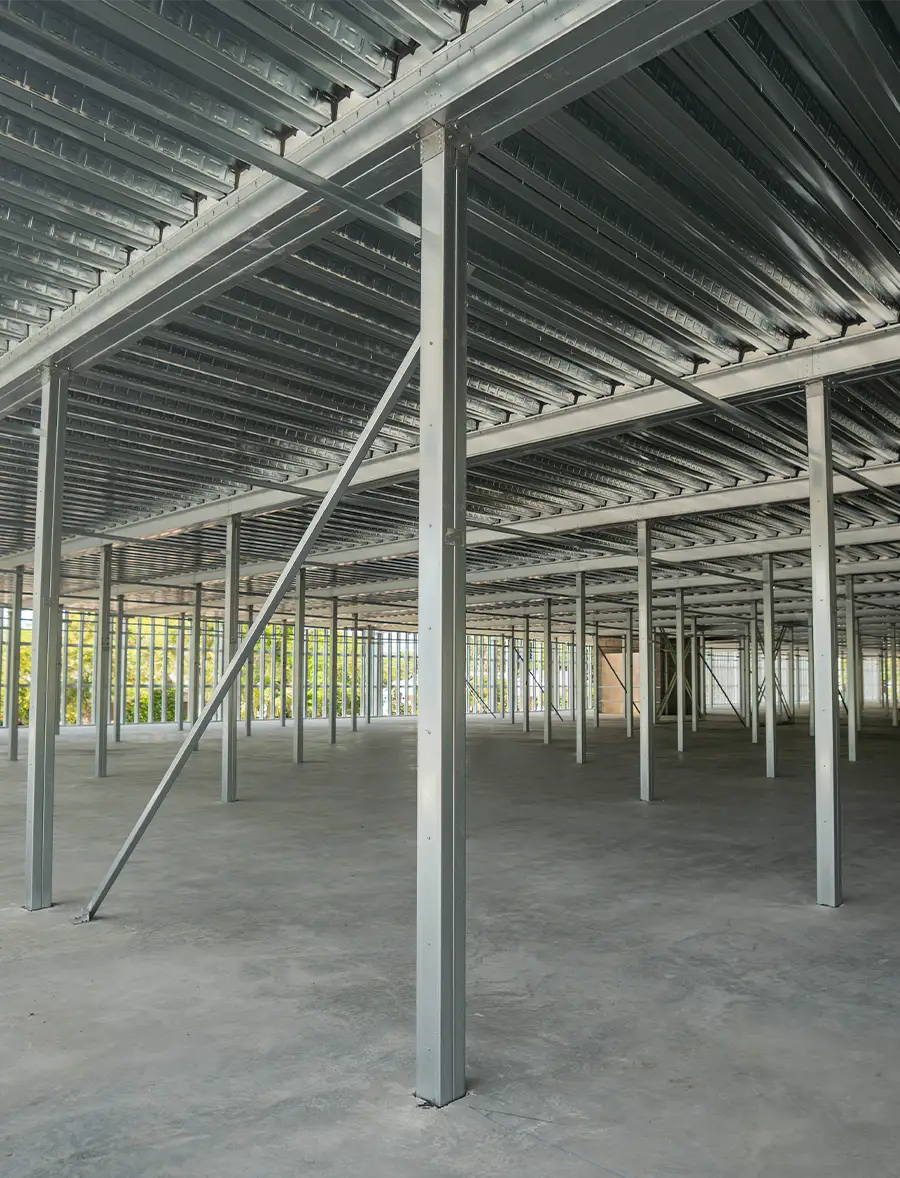
It’s crucial to note that post and beam systems may still require supplementary lateral resistance components, akin to the considerations in the light gauge bearing wall approach. Collaboration with your design team and structural engineer is paramount to address seismic and lateral resistance requirements, along with the accompanying programmatic, coordination, and engineering considerations previously outlined.
Furthermore, when incorporating lateral resistance elements into projects, careful consideration should be given to their visibility within the facility. Will these systems be exposed or concealed within walls or behind finished panels and claddings? This decision impacts not only the aesthetics but also the overall functionality and user experience within the storage facility.
However, while the building code offers new possibilities, it’s crucial to align these considerations with local zoning and planning regulations. Factors such as building height restrictions, floor area ratios, and other local ordinances can impact project feasibility. Collaboration with your design team is essential to navigate these complexities effectively, ensuring compliance while maximizing project potential.
Engaging an architect or design team with expertise in self-storage facilities can provide invaluable guidance throughout the planning, design, and construction phases. Their experience enables them to offer insights tailored to the unique challenges of multistory storage projects. Additionally, partnering with general contractors and subcontractors familiar with self-storage construction further enhances project success, ensuring seamless execution from concept to completion. By leveraging the expertise of these professionals, you can optimize your project’s outcomes and deliver a successful multistory self-storage facility.